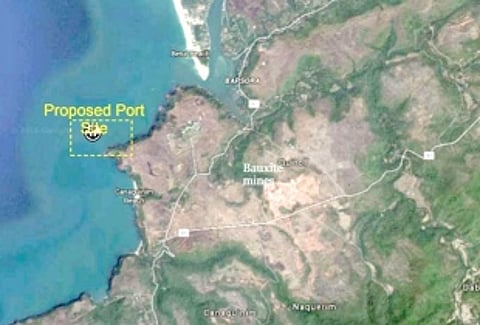
The Mormugao Port has traditionally been one of the leading iron ore exporting port of India. Due to the Supreme Court's ban on iron ore exports from Goa and subsequent restrictions on iron ore exports, the volumes handled by Mormugao have fallen sharply.
Today, Coal/Coke is a major commodity handled at the port. During the year 2013-14, more than 7.5 MT of coal was handled at Mormugao Port. There are two dedicated coal terminals (berth 6 & 7) which are being operated by private operators.
The demand for coal imports through Mormugao Port remains very strong. Along with the demand for coal, the general cargo traffic has witnessed a spurt during the past two years.
RAIL CONNECTIVITY
The Broad gauge railway system of the port serves the general cargo berths. Port Railway system is connected to south western railway through which it is also linked to Konkan Railway. Both these railway together facilitate easy access to the port from any part of the country through the vast network of broad gauge railway system.
Rail routes
• Vasco – Majorda – Madgaon – Loliem – Manglore
• Vasco – Majorda – Madgaon – Kulem – Castle Rock – Londa -Belgaum – Miraj
• Vasco – Majorda – Madgaon – Kulem – Castle Rock – Londa –Dharwad -Hubli – Hospet – Bellary
• Vasco- Cansulim – Verna – Mapusa – Pernam – Ratnagiri –Mumbai
DETAILS OF EXISTING FACILITIES
Berths 5 and 6 (Steel Products and Coal)
The Berths 5 and 6 are operated by SWPL (subsidiary of JSW).
Berth 5 is dedicated for export of steel products from JSW steel plant in Tornagallu in Vijayanagara, located about 410 km from the Mormugao Port and berth 6 is dedicated for import of coking coal that is required at the plant. The total length for berths 5 and 6 is about 450 m with an available draft of -14.1 m CD. These berths are planned for handling about 70,000 DWT vessels.
These berths are equipped with 3 mobile harbour crane having a total discharge capacity of 40,000 TPD. The receiving conveyors (from berth to stackyard) have a rated capacity of 3000 TPH and the despatch conveyors (from stackyard to despatch) have a rated capacity of 1800 TPH.
Berth 7 (Coal)
Berth 7 is leased to M/s Adani Mormugao Port Terminal Private Limited (AMPTPL). This berth with a length of 300 m has a design draft of -16.5 m CD and is designed for handling upto 160,000 DWT ships. The berth is equipped with two mobile harbour cranes, each with a rated capacity of 1750 TPH.
The fully mechanised material handling system consisting of conveyor systems, two tripping conveyors in the yard closer to the berth and one stacker cum reclaimers unit with stacking capacity of 3,500 TPH and reclaiming capacity of 2,500 TPH has been provide, in the other yard parallel to the berth.
The stackyard has a total area of 97,000 sqm with effective storage area of about 54,000 sqm. An in motion wagon loading system with a silo of capacity 4,000 T is provided for faster evacuation through rail. Two truck loading stations, with an independent hopper of capacity of 500 T, are provided for evacuation through trucks.
BCG BENCHMARKING STUDY
BCG, as part of their benchmarking study, has looked into the operation of the berths and has suggested various measures for improving the performance. The report of BCG pertaining to Mormugao Port is given in the Appendix 1. The key observations and relevant details for the port master planning are as follows:
SWPL (JSW) Terminal (Berth 6) the port has planned for deepening of the channel to level of -19.8 m CD along the approach channel, turning circle, JSW terminal and to level of -16.5 m CD at Adani terminal. It was suggested that upgradation of the terminal infrastructure should also take place for handling cape size vessels so that current throughput could be increased.
Coal Berths
Berth 6 Berth 6 is equipped with three mobile harbour cranes with connected hoppers. The coal unloaded from ship is discharged to the mobile hoppers with connected conveyor system, which takes the coal to stackyard. It is understood that while this berth substructure can cater to the higher dredged levels and the cape size ships, the existing equipment is not suitable for unloading the cape size ships.
Significant modifications to the berth superstructure would be needed for either installing the ship unloaders or providing high capacity mobile harbour cranes. This berth handles coking coal, lime stone, met coke, steam coal etc. which are brought in different parcel sizes and therefore the handling rate is also different. The average productivity achieved at this berth is the range of 25,000 T per day only, which is on a lower side considering the fully mechanised system and handymax to panamax size ships calling at the berth.
The capacity and cycle time of existing mobile harbour cranes appear to the reason for low handling rate. Considering optimal berth occupancy of only 70% for this captive berth the annual capacity works out to only 6.2 MTPA, against which it handled over 8 MT during last year but at very high berth occupancy, which resulted in significant waiting time of ships. For increasing the berth productivity there is an urgent need for the upgradation of handling system not only for increasing the handling rate but also to be able to cater to the cape size ships.
Berth 7
Berth 7 is equipped with two mobile harbour cranes, which are of much higher capacity as compared to the mobile harbour cranes provided at berth 6. This berth is highly underutilised and handled only 0.86 MT of cargo last year.
The average parcel size of ships handled was also low at about 40,000 T and therefore the productivity achieved was about 25,000 TPD as against an average of about 35,000 TPD that could be achieved at this berth based on the equipment provided.
Based on the equipment the capacity of this berth is calculated as about 8.5 MTPA, at berth occupancy of about 70%. The effective stackyard area for the berth 7 is only about 45,000 sqm. Based on the stacking arrangement at the yards, it is observed that about 0.2 MT of coal could only be stacked.
To match the berth capacity output the coal stored would need to have a turnover ratio of 48 (i.e. dwell time of 7 days), which is very high meaning that the stackyard area would remain a key constraint to the capacity of the terminal.
Berth 8 (Liquid Cargo)
Berth 8 handles various liquid cargo like Caustic Soda, Furnace Oil, H.S.D., Liquid Ammonia, motor spirit, palm oil etc.
These products are received in smaller tankers carrying low parcel size. The unloading rate is governed by on board ship’s pumps and is relatively very low. The average productivity achieved at this berth is about 9,000 TPD only. The capacity of this berth is calculated as about 2.2 MTPA at berth occupancy of about 70%.
Breakbulk Cargo Berth 5
Berth 5 mainly handles captive cargo of JSW comprising of steel products using the mobile harbour cranes or ship’s gears (when the mobile harbour cranes are deployed on berth 6).
The cargo comprises of Steel Coils (Cold Rolled), G. I. Coils, HR Sheets, HR Steel Coils (Hot Rolled), Steel Bar Rods, Steel Plates and Sheets, Steel Slabs and Steel Coils (Wire Rolled). It is observed that an average productivity achieved is about 7,000 TPD, which seems broadly in order considering the diverse nature of products handled.
Accordingly the capacity of this berth is assessed as about 1.7 MTPA at allowable berth occupancy of 70%.
However it may be noted that consequent to the deepening of the channel and the berthing areas, cape size vessel would be able to call at the port. This would mean that berth 5 and 6, which have a total berth length of 450 m would be able to handle one cape size ship only. This would affect the availability of berth 5 resulting in low throughput.
It could be seen that currently the average productivity at these berths is about 4,700 TPD only. These berths are deployed with only one mobile harbour crane and therefore most of the cargo is handled using the ship’s gear. Basis above the current total capacity of these two berths is only about 2.3 MTPA at 70% occupancy. The capacity of any multipurpose berth depends upon the type of cargo handled, the vessel parcel size, the mode of handling, the capacity of equipment deployed, the speed of evacuation and so on.
The type of cargo handled at these berths is highly variable in terms of density, mode of handling (grab, hook etc.) and therefore the handling rate achieved would significantly vary from cargo to cargo. In order to improve the productivity and hence the berth capacity additional equipment needs to be deployed. In addition any hindrances to the traffic movement from berth to yard and vice versa need to be removed. It is suggested that the cargo like granite, machinery etc. that are brought in smaller parcel sizes are handled at berth 10 using ships gears.
The annual capacity of this berth could then be taken as about 1.0 MTPA considering average productivity of about 4,000 TPD. The berth 11 should be prioritised for handling of bulk and other breakbulk cargo like alumina, wooden chips, iron ore lump etc. using the mobile harbour cranes. The existing mobile harbour crane needs to be augmented with another one and apart from that the matching equipment for transfer of cargo between yard and berth would need to be provided. This would enable higher productivity at this berth and capacity of the single berth itself could go upto 2.5 MTPA considering average productivity of about 10,000 TPD.
DETAILS OF ONGOING DEVELOPMENTS
CONSTRUCTION OF 4 LANE ROAD FROM VERNA JUNCTION ON NH17 TO THE PORT
The Tripartite Agreement between NHAI, MPT and GoG has been signed on 02.11.2014. The subject work is to be executed by Government of Goa (GoG) as per the directives of the Hon’ble Supreme Court. The GoG had appointed S. N. Bhobe & Associates, Mumbai as consultant for preparation of project reports, designs, drawings & estimates etc. for the work.
As per the tripartite agreement, a new 4 lane road is proposed to be constructed from Varunapuri Junction to the Port. It has partial elevated section and partial at grade section. It starts from Varunapuri junction and continue at grade till it reaches near Rabindra Bhavan. From there on, it has two arms. One arm takes eastern direction and comes to Gate 9 after crossing ROB. It is proposed to come at grade level near the existing temporary shed. The other arm goes straight and comes down at Grade after traversing a length of about 650 m. Then it continues further at grade and reaches at SADA junction.
AUGMENTATION OF RAILWAY NETWORK
In order to cater to the increased traffic due to various projects like Development of Berth 7, Berth 11 and west of breakwater, the rail cargo handling capacity was augmented by providing additional lines. The work of laying of additional tracks has been completed in July 2014. Construction of the Signalling building is in progress and will be completed in March 2016. Tendering work for Signalling and Telecommunication of Railway yard is in progress.
DEEPENING OF APPROACH CHANNEL FOR CAPE SIZE VESSELS AT MORMUGAO PORT
Mormugao Port has planned to deepen the existing channel to facilitate handling of capesize vessels under annuity model. The scope of the work is to deepen the outer channel from -14.4 m to -19.8 m CD and inner turning circle from -14.1 m to -19.5 m CD. The work has already been awarded to Dredging Corporation of India.
REDEVELOPMENT OF BERTHS 8, 9 & BARGE BERTHS
Mormugao Port is planning to take up the redevelopment of berths 8, 9 and barge berths to create facilities for coal and breakbulk handling. This would require shifting of the liquid handling at some other location or new berth would need to be developed.
TRAFFIC PROJECTIONS
The port of Mormugao currently handles roughly 14.7 MTPA of cargo catering primarily to the hinterlands of South Maharashtra, Northern Karnataka and Goa. One of the major bottlenecks hindering the growth of the port is the lack of good connectivity due to the Western Ghats. The port used to be the largest gateways of Iron Ore from the country which was largest export from the port but with the mining ban and Brazil taking over the China market for the supply of ore, the volumes at the port have gone down drastically.
MAJOR COMMODITIES AND THEIR PROJECTIONS
Coking Coal
The port currently imports 6.6 MTPA of coking coal from Australia and South Africa. This coking coal is primarily used by Steel plants in the vicinity of the port; JSW Vijaynagar consumes nearly 5 MTPA and JSW Dolvi consumers the remaining 1.6 MTPA.
Going into the future the volumes of steel handled at the port is expected to grow with the steel multiplier relative to the GDP. The overall traffic of coking coal is expected to grow to 14 MTPA by 2020, 19-21 MTPA by 2025 and 34-40 MTPA by 2035.
Thermal Coal
The port currently imports 1.9 MTPA of coal primarily for non-thermal power plant purposes. Going into the future the demand is expected to grow to roughly 2.6 MTPA by 2020, 3.5 MTPA by 2025 and 5-6 MTPA by 2035.
Steel
Being close to key JSW steel plants, the port is an ideal location to export finished steel products from these plants both coastal and to locations outside India. The port exports ~1 MTPA HR Steel Coils from the nearby plants, going into the future with natural steel multiplier growth we expect the volumes of exports to grow up to 2.4 MTPA by 2020, 3-4 MTPA by 2025 and 6-7 MTPA by 2035.
COASTAL SHIPPING POTENTIAL
Apart from the above mentioned traffic, there is additional opportunity of coastal shipping that can be potentially tapped. Thermal coal can form the significant share in coastal shipping while small volumes of other commodities like steel can be moved coastally
Thermal coal:
Coal can prove to be a major commodity which can be coastally shipped to the port of Mormugao. The plants of NTPC Kudgi and KPCL Bellary can shift to coastal shipping and receive their coal from the Mormugao port, if Belekeri port doesn’t come up in the near future.
See Figure 6.2 above.
CAPACITY AUGMENTATION REQUIRMENTS
The capacity augmentation requirement shall be based on the difference between the projected traffic for the particular commodity and the capacity of the port available (after debottlenecking and physical improvements) for handling that particular commodity.
SUMMARY OF DEBOTTLENECKED PORT CAPACITY
Based on the analysis of existing port infrastructure, the current capacity of the port is assessed as given in Table 7.1 below:
Berths Cargo Handled Capacity
(MTPA)
Breakbulk -
Berth 5 Steel Products 1.7
Coal - Berth 6 Coking Coal 6.2
Coal - Berth 7 Thermal Coal 8.5
Liquid - Berth 8 Oil 2.2
General Cargo -
Berths 10 & 11 Breakbulk Contain-
ers 3.5
Iron Ore - Berth
9 and barge
berths Iron Ore 0
Total 22.1
REQUIREMENT FOR CAPACITY EXPANSION
Even though prima facie it appears that the overall capacity is slightly more than the overall traffic, there is shortfall on facilities for handling specific cargo. There is also a need to improve the operational efficiency in cargo handling and storage by way of better circulation plan of traffic of breakbulk cargo.
The traffic projections indicate the significant capacity augmentation requirement for the coal unloading facilities over a period of time. Apart from that additional facilities would also be needed for steel cargo and other breakbulk cargo. The phase wise incremental facilities required are indicated in Table 7.2 below.
It may be noted that with regard to the iron ore traffic, the current market outlook does not necessitate providing any additional facility for iron ore and the small projected throughput could be handled at the moorings. However, in optimistic scenario, significant quantity of iron ore is expected to be handled at the port for which additional facilities would need to be created. As per Table 7.2 above it could be seen that additional facilities for coal unloading, breakbulk cargo and containers are required to be provided at the port in a phased manner.
ASSESSMENT OF RAIL CAPACITY
The traffic projections for any port are based on the unconstraint cargo flow in and out of the port. However, the actual cargo that could be handled at a port would be limited by least of the berth capacity, storage capacity and the evacuation capacity. In particular case of Mormugao Port, it is assessed that capacity of rail evacuation may pose a constraint to cargo handling capacity of the port.
The same is assessed as below: Presently, the port is connected to Vasco da Gama yard with a double line leading from the yard of the Port to Vasco da Gama station. The length of this link is approximately 3 km. The existing yard at the port has 6 lines and handles approximately 10-11 rakes every day. There is a space available for the expansion of this yard by another 3 lines. With the addition of these 3 lines and a properly designed yard it should be in a position to send out 30 rakes per day. A double line link between the port and Vasco da Gama yard is capable of carrying over 30 rakes for onward destinations.
However, this can only happen if Vasco da Gama yard is remodelled i.e. expansion of the yard takes place.
In other words, more full length lines would be required to be added. It is however noted that there is no space for expansion of the yard unless more land is acquired by the Indian Railways for the purpose.
If the additional land is acquired for adding another 2 to 3 lines, it should be possible to cater to the outward traffic of 30 rakes, without which the capacity may be limited to about 15 rakes only.
Vasco da Gama yard is sandwiched on both sides with heavily built up areas. Experience shows that acquisition of such areas for the projects of this type generally becomes a long drawn process.
Beyond Vasco da Gama the connectivity of Railways is only towards one direction as Vasco da Gama is a dead end. This connectivity is through a single line section for over 300 Km.
Even if we expand the yard, the single line section would pose to be a bottleneck. Railways doubling project was initiated a few years back, with railways sanctioning the grants for doubling the line from Goa to Hospet. The works from the port to Hospet at each intermediate station are at different stages of completion.
■ The stretch between Hospet and Tinai Ghat (241 km) is under progress and expected to be complete by 2017.
■ The stretch between Tinai Ghat and Castle Rock is 12.5 km long; survey work is under progress and forest land to be transferred to railway. It is expected to be complete by 2019.
■ The stretch between Castle Rock and Kulem (25 km) is one of the steepest gradients in the country making it technically challenging and is expected to complete by 2019.
■ The stretch between Kulem and MPT is 58 km long. 10 ha of land patches to be acquired however it is stalled from past 3 years due to constraints in land acquisition Doubling of the line has to be completed with last mile connectivity by 2019 in order to improve the port's evacuation capacity. Local government has to be pressurized from the centre for the completion of doubling of the line. It should be noted that the stretch between Castle Rock and Kulem of about 25 km has the distinction of having the steepest gradient (1 in 37) encountered anywhere on the Indian Railway system.
It is understood that 5 locos have to be attached to the rake passing through this section. This significantly reduces the line capacity and it is assessed that even after doubling the capacity of this stretch shall be limited to 25 to 30 rakes only.
Considering that this stretch passes from ecologically sensitive area involving Wild Life Sanctuary, tripling of the line is unlikely. Therefore the rail evacuation capacity from the port is likely to be limited to 30 rakes each way only even after completion of the proposed projects.
SCOPE FOR FUTURE CAPACITY EXPANSION
OUTER HARBOUR FOR IRON ORE/ COAL TERMINAL
With the development of the proposed 8, 9 and barge berths as well as the new liquid and passenger jetty, the port facilities would be adequate to handle the projected traffic upto 2025. In case the ban on iron ore is lifted and its traffic goes up as projected in optimistic scenario in Table 6.1 additional iron ore export berth (apart from 9A berth being planned at present) would be needed.
The ideal location for this could be in a harbour basin protected by a new breakwater towards the west side of the existing breakwater. The harbour would have deep water iron ore export berths apart from handling barge jetties for bringing iron ore through the IWT mode.
Similarly there is requirement of significant capacity augmentation for coal unloading. The facility for the same could also be provided in outer harbour, though the layout could be slightly different
MULTIPURPOSE TERMINAL AT BETUL
Bauxite mines are located at Betul about 35 km south of the Mormugao port. There are significant bauxite reserves at this location (over 200 MT). The location plan of the proposed port site and the Bauxite mines is shown in Figure 8.3 below.
Mormugao Port may explore the possibility of developing a terminal at Betul for export of Bauxite. This could either be a direct loading port for all weather or fair weather operations. Alternative a barge terminal could be planned at Betul for loading the mother ships inside the Mormugao harbour. The logistically most optimum solution could be worked out by a way of a detailed study.
SHELF OF NEW PROJECTS AND PHASING
As part of the Mormugao Port Master Plan several projects have been identified which need to be taken up in phased manner with the built up in traffic. The proposed phasing, capacity addition and the likely investments are discussed in paragraphs below. It may be noted that apart from these projects there could be several other projects which port would be implementing as part of the routine operations and maintenance of the port facilities. Further the phasing proposed is not cast in stone but could be reviewed periodically and revised based on the economic scenario and demand for port at that particular point of time.
PROJECTS TO BE COMPLETED BY YEAR 2020
The details of the projects which are envisaged to be completed by year 2020 are given below in Table 9.2
S. No. Project Name Investment Required (Cr) Capacity Addition (MTPA) Mode of Implementation
1. Road circulation plan for ease of movement of break bulk cargo 50 - Port's funds
2. Redevelopment of berths 8 and 9 – Coal Terminal 400 10.0 PPP
3. Finger Jetty at Vasco Bay for Liquid Cargo, Passenger and Fishing 80 5.0 Port's funds
4. Development of Two Berths with Connecting Flyover for Indian Navy and Coast Guard at Vasco Bay 500 - Port’s / Navy
5. Vasco Yard Expansion 25 - Port's funds
PROJECTS TO BE COMPLETED BY YEAR 2025
S. No. Project Name Investment Required (Cr) Capacity Addition (MTPA) Mode of Implementation
1. Redevelopment of berths 8 and 9 - Ore and multipurpose berths 685 15.0 PPP
2. Multipurpose Terminal at Betul 1200 6.0 PPP
PROJECTS TO BE COMPLETED BY YEAR 2035
The details of the projects which are envisaged to be completed by year 2035 are given below in Table 9.4
S. No. Project Name Investment Required (Cr) Capacity Addition (MTPA) Mode of Implementation
1. Outer Harbour for Iron Ore/ Coal Terminal 1400 30 PPP